La composición química de la arena cerámica es principalmente Al2O3 y SiO2, y la fase mineral de la arena cerámica es principalmente la fase corindón y la fase mullita, así como una pequeña cantidad de fase amorfa.La refractariedad de la arena cerámica es generalmente superior a 1800 °C y es un material refractario de aluminio y silicio de alta dureza.
Características de la arena cerámica
● alta refractariedad;
● Pequeño coeficiente de expansión térmica;
● Alta conductividad térmica;
● Forma esférica aproximada, factor de ángulo pequeño, buena fluidez y capacidad compacta;
● Superficie lisa, sin grietas, sin golpes;
● material neutro, adecuado para diversos materiales metálicos de fundición;
● Las partículas tienen alta resistencia y no se rompen fácilmente;
● El rango de tamaño de partícula es amplio y la mezcla se puede personalizar de acuerdo con los requisitos del proceso.
Aplicación de Arena Cerámica en Fundición de Motores
1. Use arena de cerámica para resolver el veteado, la adherencia de arena, el núcleo roto y la deformación del núcleo de arena de la culata de hierro fundido
● El bloque de cilindros y la culata son las piezas fundidas más importantes del motor.
● La forma de la cavidad interna es compleja y los requisitos de precisión dimensional y limpieza de la cavidad interna son altos
● Lote grande

Con el fin de garantizar la eficiencia de la producción y la calidad del producto,
● Generalmente se utiliza la producción en línea de producción de arena verde (principalmente línea de peinado hidrostático).
● Los núcleos de arena generalmente utilizan un proceso de caja fría y arena recubierta de resina (núcleo de concha), y algunos núcleos de arena utilizan un proceso de caja caliente.
● Debido a la forma compleja del núcleo de arena del bloque de cilindros y la fundición de la culata, algunos núcleos de arena tienen un área transversal pequeña, la parte más delgada de algunos bloques de cilindros y núcleos de camisa de agua de la culata es de solo 3-3,5 mm, y la salida de arena es estrecha, el núcleo de arena después de la fundición está rodeado de hierro fundido a alta temperatura durante mucho tiempo, es difícil limpiar la arena y se necesita un equipo de limpieza especial, etc. En el pasado, toda la arena de sílice se usaba en la fundición producción, lo que provocó vetas y problemas de adherencia de arena en las piezas fundidas de la camisa de agua del bloque de cilindros y la culata.Los problemas de deformación del núcleo y núcleo roto son muy comunes y difíciles de resolver.
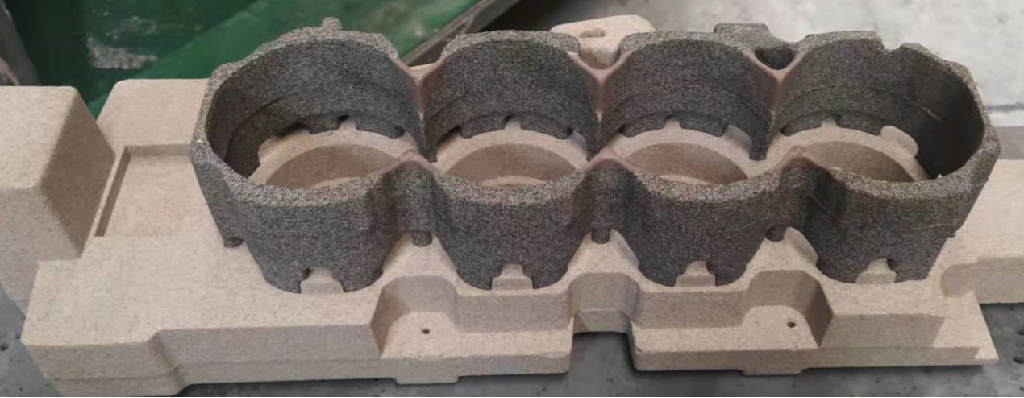
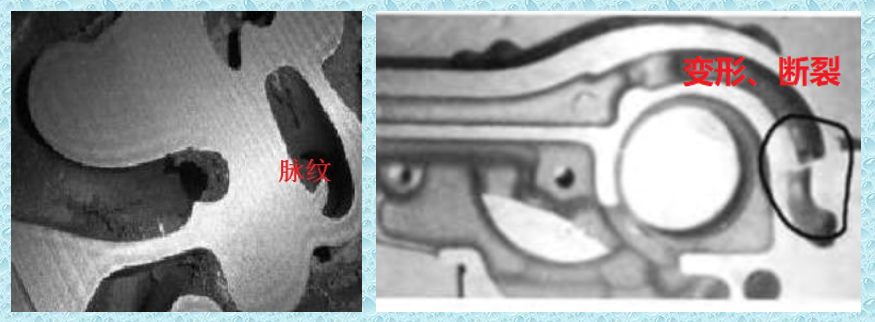
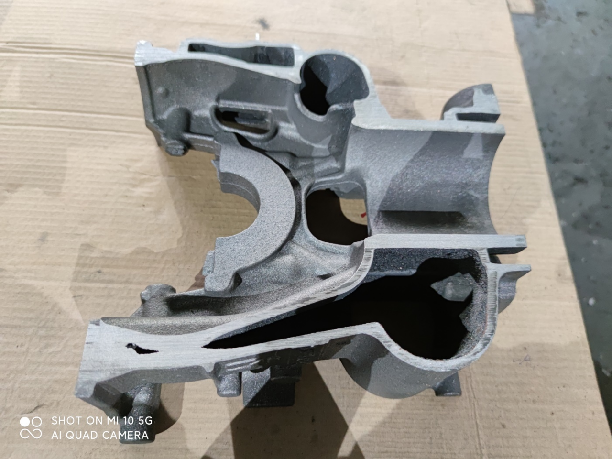
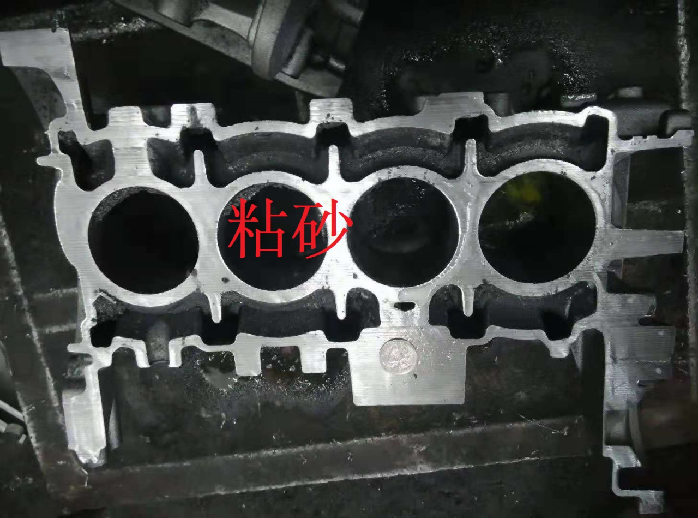
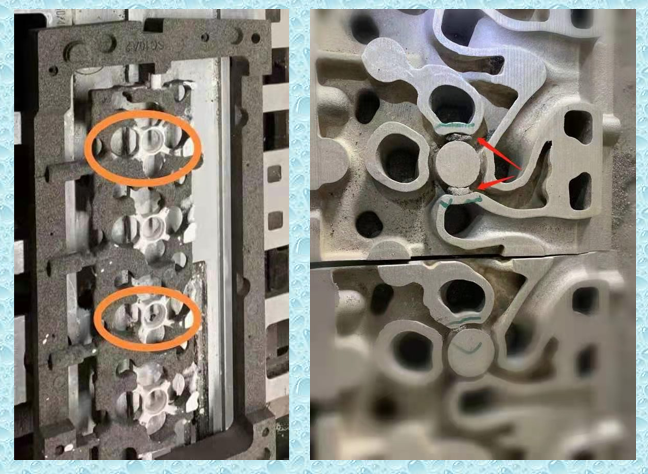
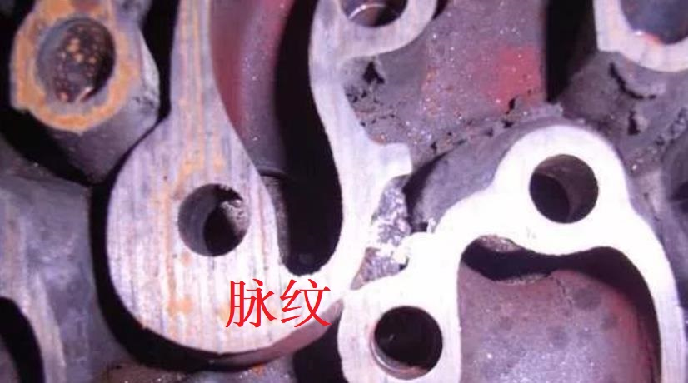
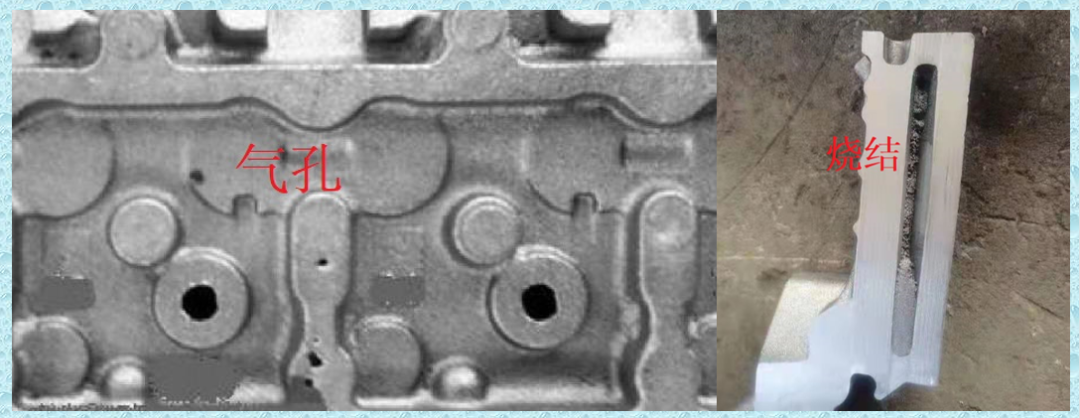
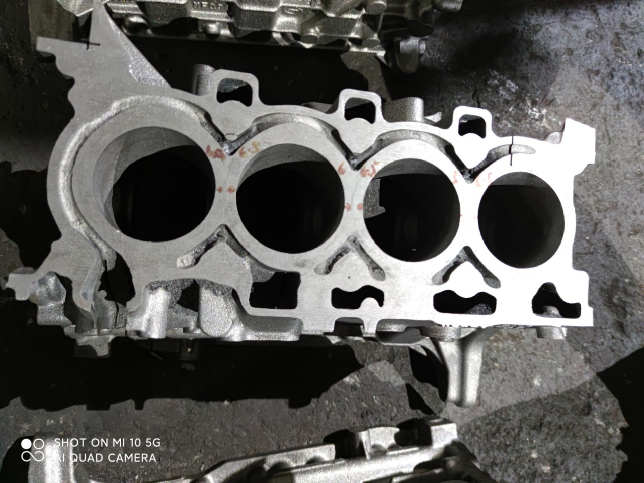
Para resolver estos problemas, a partir de 2010, algunas empresas de fundición de motores nacionales conocidas, como FAW, Weichai, Shangchai, Shanxi Xinke, etc., comenzaron a investigar y probar la aplicación de arena cerámica para producir bloques de cilindros. camisas de agua de la culata y conductos de aceite.Los núcleos de arena iguales eliminan o reducen de manera efectiva defectos como la sinterización de la cavidad interna, la adherencia de la arena, la deformación del núcleo de arena y los núcleos rotos.
Las siguientes imágenes están hechas con arena cerámica con proceso de caja fría.
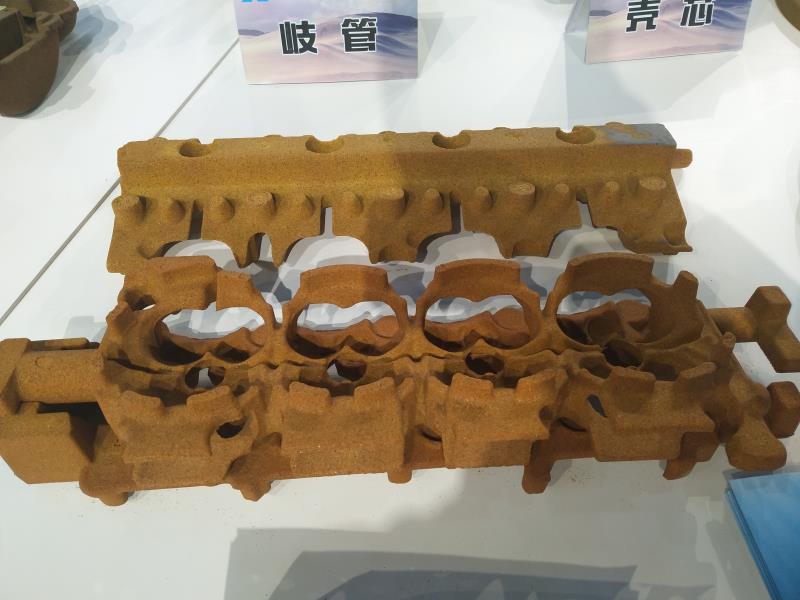
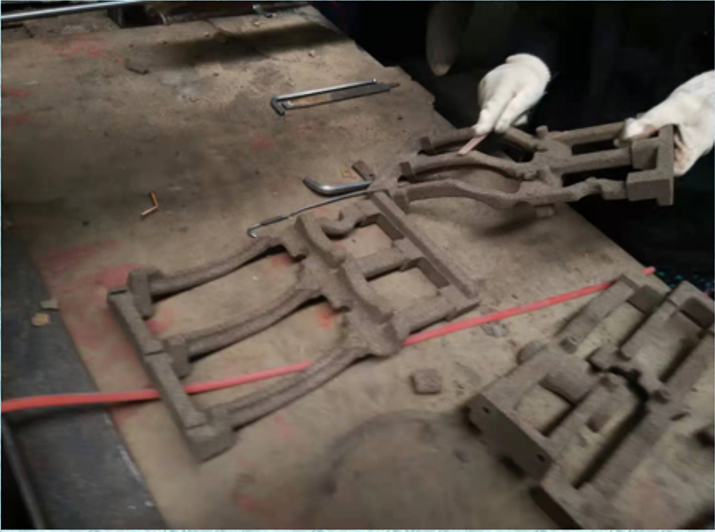
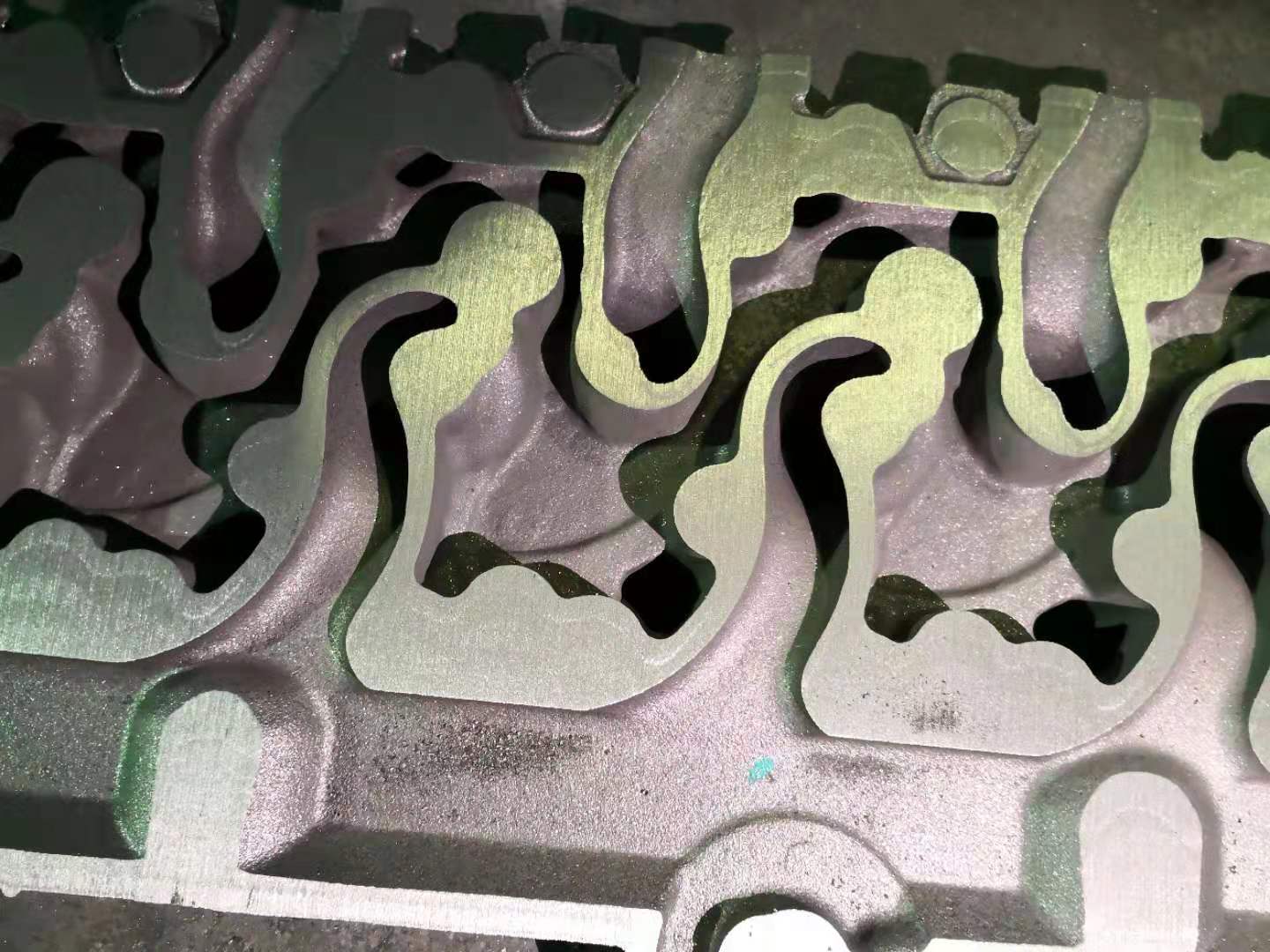
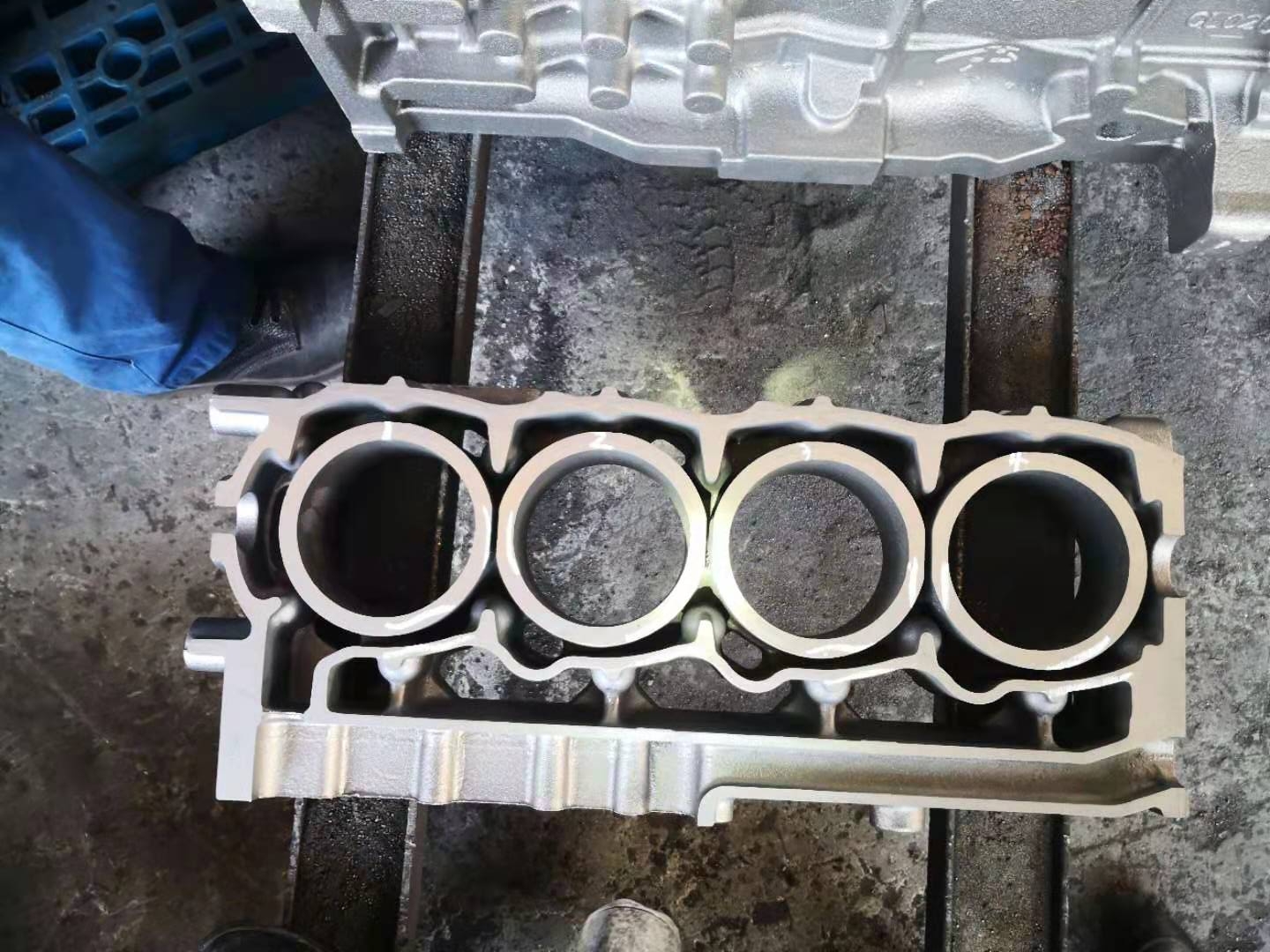
Desde entonces, la arena de depuración mezclada con arena cerámica se ha promovido gradualmente en los procesos de caja fría y caja caliente, y se ha aplicado a los núcleos de las camisas de agua de las culatas.Ha estado en producción estable durante más de 6 años.El uso actual del núcleo de arena de caja fría es: según la forma y el tamaño del núcleo de arena, la cantidad de arena cerámica añadida es del 30 % al 50 %, la cantidad total de resina añadida es del 1,2 % al 1,8 % y la la resistencia a la tracción es de 2,2-2,7 MPa.(Datos de pruebas de muestras de laboratorio)
Resumen
Las piezas de hierro fundido del bloque de cilindros y la culata contienen muchas estructuras de cavidades internas estrechas, y la temperatura de vertido es generalmente entre 1440 y 1500 °C.La parte de pared delgada del núcleo de arena se sinteriza fácilmente bajo la acción del hierro fundido a alta temperatura, como el hierro fundido que se infiltra en el núcleo de arena, o produce una reacción de interfaz para formar arena pegajosa.La refractariedad de la arena cerámica es superior a 1800 °C, mientras que la densidad real de la arena cerámica es relativamente alta, la energía cinética de las partículas de arena con el mismo diámetro y velocidad es 1,28 veces mayor que la de las partículas de arena de sílice cuando se dispara arena, que puede aumentar la densidad de los núcleos de arena.
Estas ventajas son las razones por las que el uso de arena cerámica puede resolver el problema de la adherencia de arena en la cavidad interna de las piezas fundidas de la culata.
La camisa de agua, las partes de admisión y escape del bloque de cilindros y la culata a menudo tienen defectos de vetas.Una gran cantidad de investigaciones y prácticas de fundición han demostrado que la causa raíz de los defectos de veteado en la superficie de fundición es la expansión por cambio de fase de la arena de sílice, lo que provoca estrés térmico que conduce a grietas en la superficie del núcleo de arena, lo que provoca hierro fundido. a penetrar en las grietas, la tendencia de las vetas es mayor sobre todo en el proceso de caja fría.De hecho, la tasa de expansión térmica de la arena de sílice es tan alta como 1,5 %, mientras que la tasa de expansión térmica de la arena cerámica es de solo 0,13 % (calentada a 1000 °C durante 10 minutos).La posibilidad de agrietamiento es muy pequeña en la superficie del núcleo de arena debido a la tensión de expansión térmica.El uso de arena cerámica en el núcleo de arena del bloque de cilindros y la culata es actualmente una solución simple y efectiva al problema del veteado.
Los núcleos de arena de la camisa de agua de la culata del cilindro complicados, de paredes delgadas, largos y estrechos y los núcleos de arena del canal de aceite del cilindro requieren alta resistencia (incluida la resistencia a altas temperaturas) y tenacidad, y al mismo tiempo necesitan controlar la generación de gas de la arena del núcleo.Tradicionalmente, se utiliza principalmente el proceso de arena recubierta.El uso de arena cerámica reduce la cantidad de resina y logra el efecto de alta resistencia y baja generación de gas.Debido a la mejora continua del rendimiento de la resina y la arena cruda, el proceso de caja fría ha reemplazado cada vez más parte del proceso de arena recubierta en los últimos años, lo que mejora en gran medida la eficiencia de la producción y mejora el entorno de producción.
2. Aplicación de arena cerámica para resolver el problema de la deformación del núcleo de arena del tubo de escape.
Los colectores de escape funcionan en condiciones alternas de alta temperatura durante mucho tiempo, y la resistencia a la oxidación de los materiales a altas temperaturas afecta directamente la vida útil de los colectores de escape.En los últimos años, el país ha mejorado continuamente los estándares de emisión de los gases de escape de los automóviles, y la aplicación de la tecnología catalítica y la tecnología de turboalimentación ha aumentado significativamente la temperatura de trabajo del colector de escape, superando los 750 °C.Con la mejora adicional del rendimiento del motor, la temperatura de trabajo del colector de escape también aumentará.En la actualidad, generalmente se utiliza acero fundido resistente al calor, como ZG 40Cr22Ni10Si2 (JB/T 13044), etc., con una temperatura resistente al calor de 950°C-1100°C.
Por lo general, se requiere que la cavidad interna del múltiple de escape esté libre de grietas, cierres fríos, cavidades de contracción, inclusiones de escoria, etc. que afecten el rendimiento, y se requiere que la rugosidad de la cavidad interna no sea mayor que Ra25.Al mismo tiempo, existen normas estrictas y claras sobre la desviación del espesor de la pared de la tubería.Durante mucho tiempo, el problema del grosor desigual de la pared y la desviación excesiva de la pared del tubo del colector de escape ha afectado a muchas fundiciones de colectores de escape.

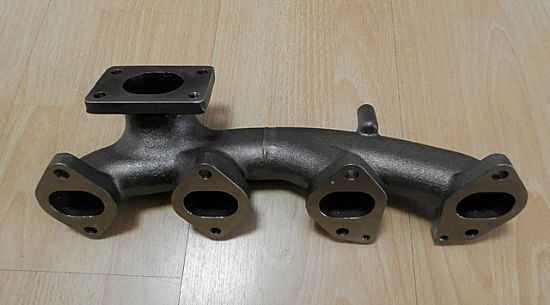
Una fundición utilizó por primera vez núcleos de arena recubiertos con arena de sílice para producir colectores de escape de acero resistentes al calor.Debido a la alta temperatura de vertido (1470-1550°C), los núcleos de arena se deformaban fácilmente, lo que resultaba en fenómenos fuera de tolerancia en el espesor de la pared de la tubería.Aunque la arena de sílice ha sido tratada con cambio de fase a alta temperatura, debido a la influencia de varios factores, todavía no puede superar la deformación del núcleo de arena a alta temperatura, lo que da como resultado una amplia gama de fluctuaciones en el espesor de la pared de la tubería. , y en casos severos, será desechado.Para mejorar la resistencia del núcleo de arena y controlar la generación de gas del núcleo de arena, se decidió utilizar arena recubierta de arena cerámica.Cuando la cantidad de resina añadida fue un 36% inferior a la de la arena recubierta de arena de sílice, su resistencia a la flexión a temperatura ambiente y la resistencia a la flexión térmica aumentaron en un 51%, 67%, y la cantidad de generación de gas se redujo en un 20%, lo que cumple con el requisitos del proceso de alta resistencia y baja generación de gas.
La fábrica utiliza núcleos de arena recubiertos de arena de sílice y núcleos de arena recubiertos de arena de cerámica para la fundición simultánea, después de limpiar las piezas fundidas, realizan inspecciones anatómicas.
Si el núcleo está hecho de arena recubierta de arena de sílice, las piezas fundidas tienen un espesor de pared desigual y una pared delgada, y el espesor de la pared es de 3,0 a 6,2 mm;cuando el núcleo está hecho de arena recubierta de arena cerámica, el grosor de la pared de la fundición es uniforme y el grosor de la pared es de 4,4-4,6 mm.como sigue la imagen
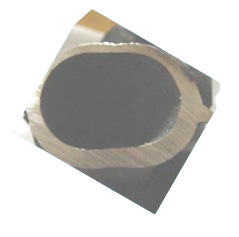
Arena recubierta de arena de sílice
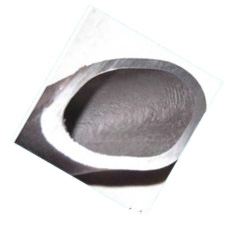
Arena recubierta de arena cerámica
La arena recubierta de arena cerámica se usa para hacer núcleos, lo que elimina la rotura del núcleo de arena, reduce la deformación del núcleo de arena, mejora en gran medida la precisión dimensional del canal de flujo de la cavidad interna del colector de escape y reduce la adherencia de arena en la cavidad interna, mejorando la calidad de tasa de fundición y productos terminados y logró importantes beneficios económicos.
3. Aplicación de arena cerámica en la carcasa del turbocargador
La temperatura de trabajo en el extremo de la turbina de la carcasa del turbocompresor generalmente supera los 600 °C, y algunos incluso alcanzan los 950-1050 °C.El material de la carcasa debe ser resistente a altas temperaturas y tener un buen rendimiento de lanzamiento.La estructura de la carcasa es más compacta, el grosor de la pared es delgado y uniforme, y la cavidad interna está limpia, etc., es extremadamente exigente.En la actualidad, la carcasa del turbocompresor se fabrica generalmente con fundición de acero resistente al calor (como 1.4837 y 1.4849 de la norma alemana DIN EN 10295), y también se utiliza hierro dúctil resistente al calor (como el estándar alemán GGG SiMo, el estándar estadounidense hierro nodular austenítico alto en níquel estándar D5S, etc.).
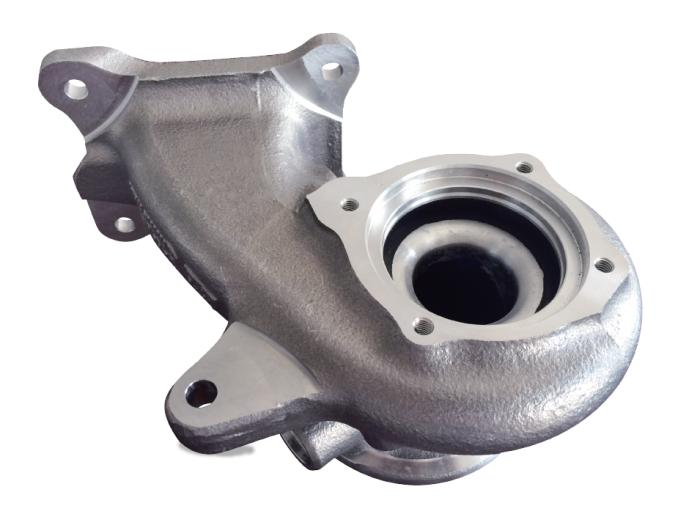
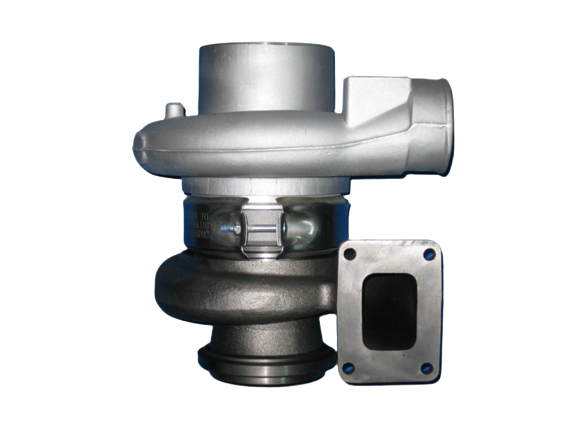
Carcasa del turbocompresor del motor de 1,8 T, material: 1,4837, a saber, GX40CrNiSi 25-12, composición química principal (%): C: 0,3-0,5, Si: 1-2,5, Cr: 24-27, Mo: máx. 0,5, Ni: 11 -14, temperatura de vertido 1560 ℃.La aleación tiene un alto punto de fusión, una gran tasa de contracción, una fuerte tendencia al agrietamiento en caliente y una alta dificultad de fundición.La estructura metalográfica de la fundición tiene requisitos estrictos sobre carburos residuales e inclusiones no metálicas, y también existen regulaciones específicas sobre defectos de fundición.Con el fin de garantizar la calidad y la eficiencia de producción de las piezas fundidas, el proceso de moldeo adopta la fundición del núcleo con núcleos de cáscara de arena recubiertos con una película (y algunos núcleos de caja fría y caja caliente).Inicialmente, se usó arena de fregado AFS50 y luego arena de sílice tostada, pero aparecieron problemas como adherencia de arena, rebabas, grietas térmicas y poros en la cavidad interna en diversos grados.
Sobre la base de la investigación y las pruebas, la fábrica decidió utilizar arena cerámica.Inicialmente compró arena recubierta terminada (100% arena cerámica), y luego compró equipos de regeneración y recubrimiento, y optimizó continuamente el proceso durante el proceso de producción, usó arena cerámica y arena de lavado para mezclar arena cruda.En la actualidad, la arena recubierta se implementa aproximadamente de acuerdo con la siguiente tabla:
Proceso de arena con revestimiento de arena de cerámica para la carcasa del turbocompresor | ||||
Tamaño de arena | Tasa de arena cerámica % | % de adición de resina | Resistencia a la flexión MPa | Salida de gas ml/g |
AFS50 | 30-50 | 1.6-1.9 | 6.5-8 | ≤12 |
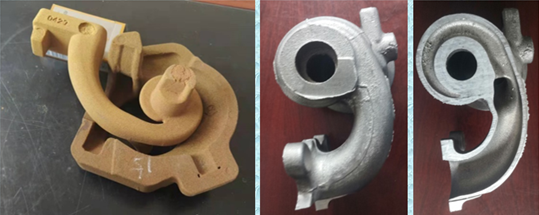
En los últimos años, el proceso de producción de esta planta ha funcionado de manera estable, la calidad de las piezas fundidas es buena y los beneficios económicos y ambientales son notables.El resumen es el siguiente:
a.El uso de arena cerámica, o el uso de una mezcla de arena cerámica y arena de sílice para fabricar núcleos, elimina defectos como la adherencia de la arena, la sinterización, el veteado y el agrietamiento térmico de las piezas fundidas, y logra una producción estable y eficiente;
b.Fundición de núcleo, alta eficiencia de producción, baja relación arena-hierro (generalmente no más de 2:1), menor consumo de arena cruda y menores costos;
C.El vertido del núcleo favorece el reciclaje y la regeneración general de la arena residual, y la recuperación térmica se adopta de manera uniforme para la regeneración.El rendimiento de la arena regenerada ha alcanzado el nivel de arena nueva para arena de lavado, lo que ha logrado el efecto de reducir el costo de compra de arena cruda y reducir la descarga de desechos sólidos;
d.Es necesario comprobar con frecuencia el contenido de arena cerámica en la arena regenerada para determinar la cantidad de arena cerámica nueva añadida;
mi.La arena cerámica tiene forma redonda, buena fluidez y gran especificidad.Cuando se mezcla con arena de sílice, es fácil causar segregación.Si es necesario, se debe ajustar el proceso de disparo de arena;
F.Al cubrir la película, trate de usar resina fenólica de alta calidad y use varios aditivos con precaución.
4. Aplicación de arena cerámica en la culata de aleación de aluminio del motor
Con el fin de mejorar la potencia de los automóviles, reducir el consumo de combustible, reducir la contaminación de los gases de escape y proteger el medio ambiente, los automóviles livianos son la tendencia de desarrollo de la industria automotriz.En la actualidad, las piezas fundidas de motores de automóviles (incluidos los motores diésel), como los bloques de cilindros y las culatas, generalmente se funden con aleaciones de aluminio, y el proceso de fundición de los bloques de cilindros y las culatas, cuando se utilizan núcleos de arena, fundición por gravedad en moldes metálicos y fundición a baja presión. casting (LPDC) son los más representativos.
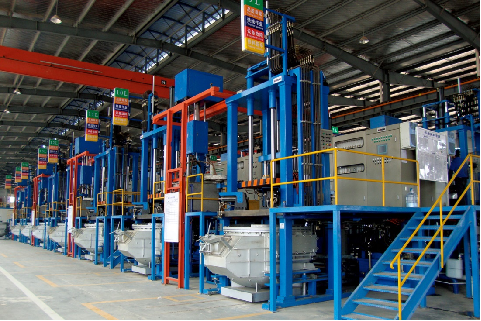
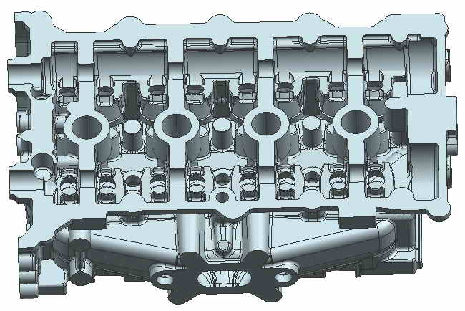
El núcleo de arena, la arena recubierta y el proceso de caja fría del bloque de cilindros de aleación de aluminio y las fundiciones de cabeza son más comunes, adecuados para características de producción a gran escala y de alta precisión.El método de uso de arena cerámica es similar a la producción de culatas de hierro fundido.Debido a la baja temperatura de vertido y la pequeña gravedad específica de la aleación de aluminio, generalmente se usa arena de núcleo de baja resistencia, como un núcleo de arena de caja fría en una fábrica, la cantidad de resina agregada es 0.5-0.6% y la resistencia a la tracción es 0,8-1,2 MPa.Se requiere arena de núcleo Tiene buena colapsabilidad.El uso de arena cerámica reduce la cantidad de resina añadida y mejora en gran medida el colapso del núcleo de arena.
En los últimos años, con el fin de mejorar el entorno de producción y mejorar la calidad de las piezas fundidas, hay cada vez más investigaciones y aplicaciones de aglutinantes inorgánicos (incluidos el vidrio soluble modificado, aglutinantes de fosfato, etc.).La imagen a continuación es el sitio de fundición de una fábrica que utiliza culata de cilindro de aleación de aluminio de arena con núcleo de aglutinante inorgánico de arena cerámica.
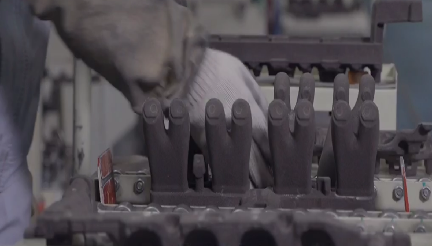
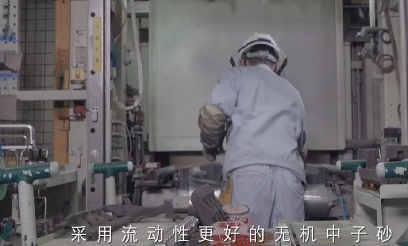
La fábrica utiliza un aglutinante inorgánico de arena cerámica para hacer el núcleo, y la cantidad de aglutinante agregado es del 1,8 al 2,2%.Debido a la buena fluidez de la arena cerámica, el núcleo de arena es denso, la superficie es completa y lisa y, al mismo tiempo, la cantidad de generación de gas es pequeña, mejora en gran medida el rendimiento de las piezas fundidas, mejora la colapsabilidad de la arena del núcleo. , mejora el entorno de producción y se convierte en un modelo de producción verde.
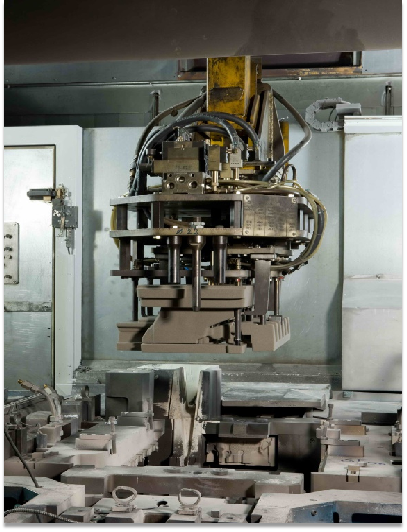
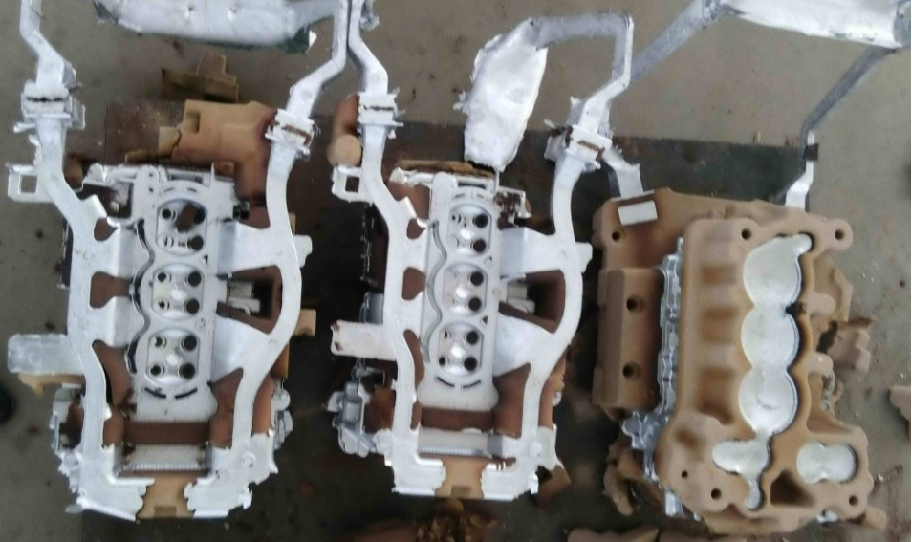
La aplicación de arena cerámica en la industria de fundición de motores ha mejorado la eficiencia de producción, mejorado el entorno de trabajo, solucionado los defectos de fundición y logrado importantes beneficios económicos y buenos beneficios ambientales.
La industria de fundición de motores debe continuar aumentando la regeneración de arena de núcleo, mejorar aún más la eficiencia de uso de la arena cerámica y reducir las emisiones de desechos sólidos.
Desde la perspectiva del efecto del uso y el alcance del uso, la arena cerámica es actualmente la arena especial de fundición con el mejor rendimiento integral y el mayor consumo en la industria de fundición de motores.
Hora de publicación: 27-mar-2023